朱锦(大豆基木材胶黏剂研究项目负责人)说:
2006年底,我携全家人回国探亲。在老家,几个朋友知道我做塑料,就约我到临沂的废旧塑料回收厂参观。参观完废旧塑料厂后,我们开车去吃午饭,结果在经过临沂市西郊区的地方,我突然看到了一大片白花花的东西。我问朋友那是什么东西,朋友告诉我这些是木皮做胶合板用的。我就追问了一句“临沂做胶合板吗?”,于是同行的朋友骄傲地告诉我,临沂是全国最大的胶合板生产基地,周围所有的杨树都是用来做胶合板的。我接着又问生产的胶合板用不用胶黏剂,有没有气味,朋友说气味很大而且让人流眼泪。于是,我告诉我的朋友,这是甲醛的原因,并提出想到胶合板生产厂家看一看。经过朋友联系,我们直接去了一家胶合板生产厂家。一进大门我就闻到甲醛的气味,等进了车间,甲醛气味之大让我马上泪流满面,只能朦胧地看到几十个工人正在车间里做工。我问工人怎么能在厂里呆得住,工人说适应了。出来后我问工厂老板,工人长期在车间干活身体是不是会出问题,有没有防护措施。老板说所有的工人他只准许在厂里干两年,然后换工人。我听后心情非常沉重。尽管我没有做过木材胶黏剂,但是我学的高分子科学是与胶黏剂有关的。作为一名专业的科研工作者,我感到有责任解决这个问题。当时我就对同行的朋友说我要做无醛木材胶黏剂,哪怕是做出来不赚一分钱,我也要做它。随着我对甲醛危害的进一步了解,更加坚定了我要做出无醛木材胶黏剂的决心。
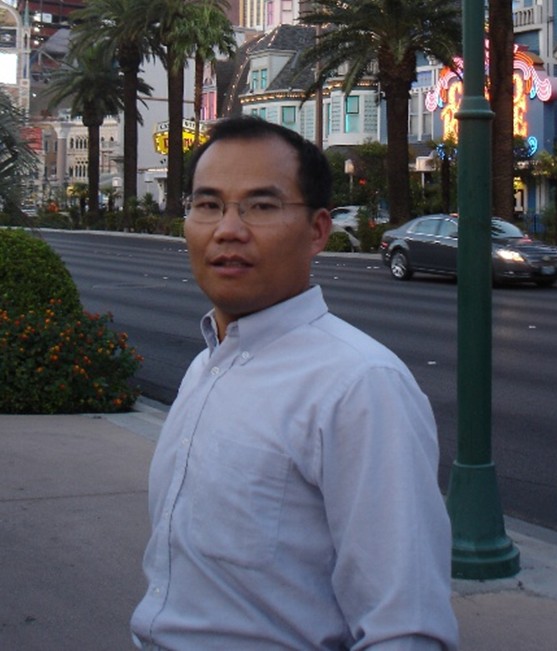
等我回到美国后,我就开始了无醛木材胶黏剂的文献检索。这件事说起来容易,做起来却发现非常困难。其时,世界各国都在研究这种新胶黏剂,其中研究最多的是以豆蛋白作为原材料做胶粘剂,于是我也选择研发豆蛋白质木材胶黏剂。当时摆在我面前最大的困难是没有试验条件,因为我所在的公司不做胶黏剂方面的研究,没有条件可以利用,况且这是我自己的研究兴趣,也不能在公司做试验。为此,我只能自己创造试验条件在家里做。家里不可能有冷压机和热压机,于是我选用烤肉的烤箱作为加热源,用一个简易夹具作为压机压制木块,再用水煮试验来判定小木块的耐水性,我就是在这种条件下开始的试验。由于白天要工作,我就利用晚上和周末做试验。开始,试验很不顺。一方面因当时没有其它手段来判定胶黏剂的好坏,而水煮的办法很难判断每次配方改进的细微变化;另一方面是我当时并不了解胶合板的制造工艺,从美国的家中做出的蛋白胶黏剂,没有考虑冷压和涂胶的工艺,拿到国内工厂使用时发现胶黏剂的固含量太低,无法涂胶。后来我知道,使用纯蛋白做原材料,虽然胶合强度和耐水性没问题,但固含量没法提上去。后来我试着改用豆粉,但发现耐水性达不到要求,同时胶黏剂的初粘性也不好,且涂胶性能和冷压都达不到要求。后来几经试验,我想到自己做过高分子纳米复合材料,使用粘土(粘土是片层结构,每一片的厚度是一纳米)可以提高高分子的耐热性和熔体强度(粘度),所以我感到粘土有可能增加胶黏剂的初粘性和耐水性。后来的试验结果证明,通过添加粘土形成纳米插层结构,初粘性和耐水性可获得大幅度提高。以此为基础,我也彻底解决了胶黏剂的冷压问题并最终完成小试试验。总之,胶黏剂的配方是在非常艰难的历程中实现的。
高玲玲(朱锦的妻子)说:
自从朱锦开始决定做胶粘剂,我就自觉的成为帮手,把寻找试验工具和材料的任务承担下来。在寻找试验工具方面,当时能想到工具主要有两个:烘箱和压力夹子。于是我到商场里买了一个烘箱,同时还买了一只200摄氏度的温度计用来精确测量烘箱里的温度。但压力夹子有点难解决,因为在商场里没有可精确控制压力的夹子。最后到HOME DEPOT买了很多夹子,最后试验中发现只有一个勉强可用(等到这次归国收拾行李时,我发现家里除了几大箱子胶合板样品,最多的就是夹子了,各式各样的)。在寻找材料方面,为了收集试验所需要的木片,我们的孩子那时只吃冰棒,因为最开始的胶合试验板是用冰棒棍子复合的(好在美国的冰棒种类很多,孩子也喜欢吃,收集起来也还算顺利),而且也并不像最终展示的这种纵横交叉叠合的样子,那时我们做的是顺纹复合板,作为外行的我们并没有发现其中的不妥,加上我们一开始选择的合作工厂给他们日本客户提供的正是顺纹的异型板材,所以在很长一段时间内,我们做的试验都是顺纹的胶合板(其他的专家却以为我们是有目的有选择的做顺纹胶合板)。当我拿到断裂强度大于6的数据时,我是多么高兴呀?因为0.7就是合格了。你可以想象的。行业的人可能知道,顺纹的胶合强度一般会比纵横交错的大2倍以上。谁让我们是外行!
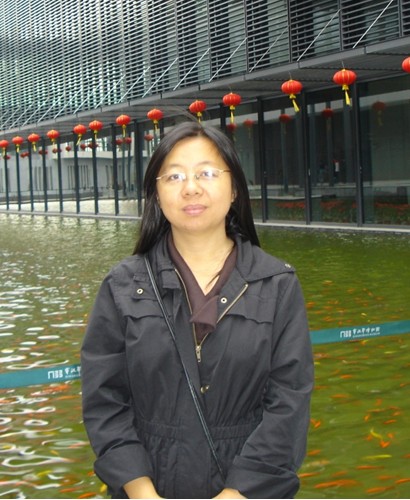
第一个试验配方基本锁定之后,我就开始了回国到临沂去做中试。首先,我的的任务是购买一台带压力表头的小型热合机。但是这种机器在市场上没有现成的产品,于是我四处打听,包括到北京的中国林业科学研究院去参观(他们所用的机器不仅多是国外进口,并且也很老旧,另外热合的面积也小)。经过不懈的寻找,我发现一台国产的试验用热合机,但和厂商联系后发现,他们不仅收费挺高,而且供货时间过长,于是最后决定自己设计一个。临沂市有很多成熟的大型板材机生产厂家,在我的一位朋友的帮助下,我们在参观了几台市场上在用的大型板材热合机,并对各项参数要求有了一定的了解之后,找到一个当地的生产厂为我们定制了自行设计的热合机,虽然他们的产品最终离我的指标要求有一定的差距,但是他们的热情服务态度以及迎难而上的作风,让我们在四个星期后拿到了机器,开始了真正意义上的中试。自己购买的买试验小用具,请朋友代购的原料、药品,尝试过的各种用于搅拌的机器(食品料理机、豆浆机,甚至还有洗衣机),还有摆满我弟弟家的阳台的瓶瓶罐罐,写到这里,我想再次大喊一声:我们是外行。没有专业的试验室,没有专业的仪器设备,甚至也没有专业的人员。我们试验做的曾经很狼狈、很辛苦。
之后的两年时间里,我陆续回国几次,有时候是做中试试验,有时候候是联系企业尝试走大型生产线,也有时候是全国范围做调研,宣传我们的板材,做开发市场的准备。在中试过程中,朱锦也进一步调整着他试验的配方,这其中有一次主要原料的大调整以及无数次的助剂调整。每一次材料性能的提高都让我们很受鼓舞,每一次不理想的反馈都是朱锦改变下一步方案的前提基础。可是大型生产线的试生产却很不顺利,面对失败,每次失败都原因不明,我们分析归结起来的原因可能是:工艺参数不合适,原料有变化等,因为每次都是在现有的生产线上添加我们的几块大板。但这种分析猜测出来的可能缺少可控的因素,朱锦的进一步试验变得很迷茫,因为他远在美国家中,做的试验结果很好,而中国的生产线上做试验,参数不可控,原料不可控,生产条件不可控,每次出现的问题也不一样。试验就这样遇到了瓶颈,而这也是促使朱锦决定归国的一个重要原因。
刘小青(朱锦的同事)说:
真正开始接触大豆基木材胶黏剂的时间应该在2010年1月,也就是我回国加入朱锦老师带领的生物基高分子材料研究团队的2个月之后。当时听完他在美国研究大豆基木材胶黏剂的动机、过程和结果介绍之后,我感到非常的激动和兴奋,并在一股跃跃欲试的冲动之下开始了文献查阅和实验准备工作。我的想法很简单:有这样好的研究课题,坚实的研究基础和优秀的研究团队,我一定要尽我所能把这个项目做好,最终把该技术实现产业化!
好的项目总会有好的出口,在所领导的关怀和支持之下,这项技术在2010年3月26日成功转移给了宁波八益实业有限公司。根据合同,我们要在六个月内完成从小试到中试再到商业化试生产的整个过程,任务之重,压力之大可想而知。为此,朱锦老师专门成立了以我为主的技术攻坚团队,全面负责该项目的产业化实施。这对于一直在大学或研究所从事基础研究的我来说,无疑是一个巨大的挑战。
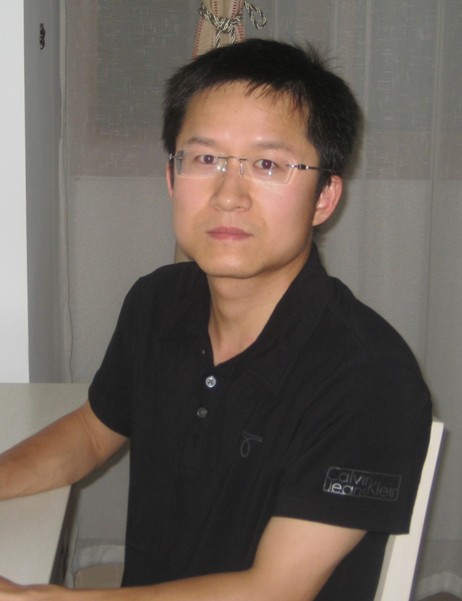
对胶合板的生产设备一窍不通、闻所未闻,对车间的基础建设感到茫然,更没有从事产业化项目开发的经验。怎么办?学习、咨询、再学习,成了我的唯一出路。为此,设备制造厂家、胶合板生产厂家和行业内研究人员都成了我咨询和学习的对象。值得欣慰的是在大家的共同努力之下,我们仅仅用了三个多月的时间,就将处于一片废墟状态的破旧厂房改造成了窗明几净的中试基地,同时完成了整套中试装置的订购、安装和调试工作,也掌握了所有设备的操作方法和胶合板生产的整套工艺。
7月初,我带领攻坚团队在炎炎酷暑中开始了在中试基地的试验工作。产业化项目不同于实验室的基础研究,它在注重实验现象记录、实验数据分析和配方调整的同时,更加注重的是工艺参数和过程在现实生产中的可行性和市场可接受度,这就需要我们尽可能地模拟和接近现实的生产过程,也因此每天大量的试验和结果的重现性显得尤为重要。结果分析、配方和工艺调整、实验重复成为我们每天必须遵守的法则。一份耕耘,一份收获,经过两个多月的高温作业,我们终于在8月底摸索、建立了一整套生产工艺和参数,并在中试设备上连续试制出了几批完全满足国家标准的无醛胶合板,且通过了国家权威机构的质量检测,为生物基无醛胶的中试画上了圆满的句号!
“完成中试不是最终目的,我们的目标是让这种无醛胶真正的实现产业化,走向市场,让我国消费者最终告别甲醛污染之苦,尽一份科技工作者应尽的职责!”这是朱锦老师和整个研发团队的誓言和目标。于是我又带领攻坚团队成员开始了在德华兔宝宝公司的试生产工作。由于兔宝宝工厂缺乏相应的制胶设备,并存在其它一些制约因素,我们每天早上六点钟就赶到中试基地制备胶黏剂,然后再驱车赶往湖州德清试制胶合板材,每次完成当天任务回到材料所都已经是凌晨两点多,说是披星戴月,一点也不为过。辛苦没有白费,在经过连续几次稳定的试生产之后,德华兔宝宝的研发人员完全认同了我们的生物基无醛胶黏剂技术。
小试成功,中试成功,试生产成功,批量化生产将是“临门一脚”。就在此时,美国某跨国公司的采购人员找到我们,“你们需要在一个月之内生产5吨无醛胶,并制备30M3无醛胶合板样板,然后送往美国进行检测,这样才能得到本公司的认可”供职于该公司的王经理如是说。就当时的情况,我们只有试验用的制胶设备,日生产能力不足100公斤,进行批量生产必须设计、订购工业化制胶设备。“一个月之内生产5吨无醛胶”,是对无醛胶生产工艺稳定性、重复性的一次考验,同时也是产品尽快真正商业化的一个机遇。于是这年10月底,我又带领攻坚团队前往江苏省泗阳县开始批量化生产。然而由于期间北方地区突然大幅度降温,导致我们生产的第一批板材质量不合格!同样的配方,同样的工艺,出现了不同的结果,这对当时的我们无异于是一个打击。幸运的是,那些经验丰富的一线生产技术人员在听取了我的过程分析之后,马上指出:“天气寒冷,胶水的流动性和对板材的渗透性都会变差,你们必须调整和摸索新的涂胶工艺”。当时已是接近春节,工厂任务繁重加上工人回家过节,使得合作厂家难以派出专门的工人配合试验。要在短时间内,在工厂现场摸索新的工艺,谈何容易。说实话,我们当时多次考虑过放弃,但是想到这次生产的重要性和我们以前的辛勤付出,大家最终还是选择了坚持。“不成功,便成仁”成了我们劳累之余的调侃,也是大家互相勉励的口号。几天实验下来,大家都不同程度的出现了体力透支现象。累了,就地坐下;困了,躺在木皮上休息片刻,以至于很多工人开始议论:“听说他们都是研究生,怎么还干这样的活,哪有知识分子的样子啊?”经过将近一周的苦战,我们终于找到了气温极低情况下的工艺参数,又一次成功得到了合格的胶合板材。然而按照我们给别人的承诺,只剩下四天时间,在剩下的四天里,设备调制几吨胶黏剂并制备30 M3的胶合板,这几乎是不可能完成的任务。这种情况下,也许是我们的行动、我们的选择、我们的精神感动了工厂的领导,厂方终于决定停掉自己的一条生产线,给我们配备足够的工人协助我们生产。经过各方的努力,30 M3生物基无醛胶合板芯板终于按时、保质地装上了开往美国的货船!两个月之后,经过美国公司的严格检验,我们的样板各项指标完全符合标准。至此,艰辛而曲折的无醛胶产业化实施过程在整个团队成员的共同努力、全力协作和辛勤付出下最终取得了成功。
朱锦说:
大豆基无醛木材胶黏剂从最开始的研制到今天产品的产出,经历了风风雨雨的岁月。除了我的家人在不同程度上参与了这项工作外,在这期间还有很多人给予我们帮助和支持。他们包括:我们在北京的朋友赵亚赟和曹小晶,是他们帮助我们申请专利,安排我们到广州、安徽、南京等地参观企业;临沂的朋友宋启华,是他做了早期的工作,投入了大量的人力和物力;临沂的邵明坤老师、李超、樊文祥、李合章则为本项目的顺利进行做了大量的工作;济南的宋佩参与了先期的市场调研。在这里我想对这些参与者表示最衷心的感谢!特别是归国后,我的这一研究得到了中科院宁波研究所以及高分子事业部领导和同仁的大力支持和帮助。十分感谢八益实业有限公司徐益忠董事长的慧眼识珠,也十分感谢感谢中科院、宁波市等各级领导的关心和支持。当然,没有生物基高分子研究团队全体成员的辛勤努力,也不会有该胶黏剂的今天。最后感谢包括新闻媒体在内的社会各界人士的关注和支持。衷心希望我们的无醛胶黏剂能够真正惠及消费者,免除甲醛带来的危害。